Q7. The president of Rose Bowl Enterprises, Desmond Howard, projects the firms aggregate DEMAND requirements over the next 8 months as follows: These are the monthly DEMAND, not production. MONTH JAN FEB MAR APR MAY JUN JULY AUG DEMAND 1,400 1,600 1,800 1,800 2,200 2,200 1,800 1,800 PRODUCTION 1,600 from December INVENTORY 200 from Dec plus 200 His operations manager is considering a new plan, which begins in January with 200 units on hand. Stockout cost of lost sales is $100 per unit. Inventory holding cost is $20 per unit per month. Ignore any idle time costs. The plan is called plan A. Plan A: Vary the workforce level to execute a strategy that produces the quantity demanded in the prior month. The December demand was given as 1,600 units per month. Therefore, the production for JAN will be 1,600. However, only 1,400 are needed. Therefore, the extra 200 produced go into inventory and there is a holding cost for inventory. Also, per the above, you already have 200 units in inventory from December, so the total would now be 400 units in inventory at the end of January. The production for FEB would be Demand from JAN. So, production for FEB would be 1,400 units. The production for March would be equal to the Demand from February... and so on. The cost of hiring additional workers is $5,000 per 100 units. The cost of laying off workers is $7,500 per 100 units. For example, we are told that production in December was 1,600 units and that production in January will be 1,600 units as well. Therefore, producing 1,600 to producing 1,600 means no change in hiring or layoffs for January therefore no additional costs except for the inventory holding costs. However, since the production in January is 1,600 and the production in February is 1,400, that is 200 units less meaning a layoff off 200 units times $7,500 as a layoff cost. So, when production goes up in a month, there is a hiring cost, when production goes down, there is a layoff cost. Evaluate the plan by computing the total costs of hiring, layoffs, stockouts and inventory. Create a table like the one above to show your values. Note that this is a CHASE strategy.
Q7. The president of Rose Bowl Enterprises, Desmond Howard, projects the firms aggregate DEMAND requirements over the next 8 months as follows: These are the monthly DEMAND, not production. MONTH JAN FEB MAR APR MAY JUN JULY AUG DEMAND 1,400 1,600 1,800 1,800 2,200 2,200 1,800 1,800 PRODUCTION 1,600 from December INVENTORY 200 from Dec plus 200 His operations manager is considering a new plan, which begins in January with 200 units on hand. Stockout cost of lost sales is $100 per unit. Inventory holding cost is $20 per unit per month. Ignore any idle time costs. The plan is called plan A. Plan A: Vary the workforce level to execute a strategy that produces the quantity demanded in the prior month. The December demand was given as 1,600 units per month. Therefore, the production for JAN will be 1,600. However, only 1,400 are needed. Therefore, the extra 200 produced go into inventory and there is a holding cost for inventory. Also, per the above, you already have 200 units in inventory from December, so the total would now be 400 units in inventory at the end of January. The production for FEB would be Demand from JAN. So, production for FEB would be 1,400 units. The production for March would be equal to the Demand from February... and so on. The cost of hiring additional workers is $5,000 per 100 units. The cost of laying off workers is $7,500 per 100 units. For example, we are told that production in December was 1,600 units and that production in January will be 1,600 units as well. Therefore, producing 1,600 to producing 1,600 means no change in hiring or layoffs for January therefore no additional costs except for the inventory holding costs. However, since the production in January is 1,600 and the production in February is 1,400, that is 200 units less meaning a layoff off 200 units times $7,500 as a layoff cost. So, when production goes up in a month, there is a hiring cost, when production goes down, there is a layoff cost. Evaluate the plan by computing the total costs of hiring, layoffs, stockouts and inventory. Create a table like the one above to show your values. Note that this is a CHASE strategy.
Practical Management Science
6th Edition
ISBN:9781337406659
Author:WINSTON, Wayne L.
Publisher:WINSTON, Wayne L.
Chapter9: Decision Making Under Uncertainty
Section: Chapter Questions
Problem 46P
Related questions
Question

Transcribed Image Text:Q7. The president of Rose Bowl Enterprises, Desmond Howard, projects the firms aggregate DEMAND
requirements over the next 8 months as follows: These are the monthly DEMAND, not production.
MONTH
JAN
FEB
MAR
APR
MAY
JUN
JULY
AUG
DEMAND
1,400
1,600
1,800
1,800
2,200
2,200
1,800
1,800
PRODUCTION
1,600 from December
INVENTORY
200 from Dec plus 200
His operations manager is considering a new plan, which begins in January with 200 units on hand.
Stockout cost of lost sales is $100 per unit. Inventory holding cost is $20 per unit per month. Ignore any
idle time costs. The plan is called plan A.
Plan A: Vary the workforce level to execute a strategy that produces the quantity demanded in the prior
month. The December demand was given as 1,600 units per month. Therefore, the production for JAN
will be 1,600. However, only 1,400 are needed. Therefore, the extra 200 produced go into inventory and
there is a holding cost for inventory. Also, per the above, you already have 200 units in inventory from
December, so the total would now be 400 units in inventory at the end of January. The production for
FEB would be Demand from JAN. So, production for FEB would be 1,400 units. The production for March
would be equal to the Demand from February... and so on.
The cost of hiring additional workers is $5,000 per 100 units. The cost of laying off workers is $7,500 per
100 units. For example, we are told that production in December was 1,600 units and that production in
January will be 1,600 units as well. Therefore, producing 1,600 to producing 1,600 means no change in
hiring or layoffs for January therefore no additional costs except for the inventory holding costs.
However, since the production in January is 1,600 and the production in February is 1,400, that is 200
units less meaning a layoff off 200 units times $7,500 as a layoff cost. So, when production goes up in a
month, there is a hiring cost, when production goes down, there is a layoff cost. Evaluate the plan by
computing the total costs of hiring, layoffs, stockouts and inventory. Create a table like the one above
to show your values. Note that this is a CHASE strategy.
Expert Solution

This question has been solved!
Explore an expertly crafted, step-by-step solution for a thorough understanding of key concepts.
Step by step
Solved in 2 steps with 2 images

Recommended textbooks for you
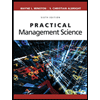
Practical Management Science
Operations Management
ISBN:
9781337406659
Author:
WINSTON, Wayne L.
Publisher:
Cengage,
Marketing
Marketing
ISBN:
9780357033791
Author:
Pride, William M
Publisher:
South Western Educational Publishing
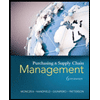
Purchasing and Supply Chain Management
Operations Management
ISBN:
9781285869681
Author:
Robert M. Monczka, Robert B. Handfield, Larry C. Giunipero, James L. Patterson
Publisher:
Cengage Learning
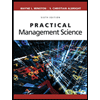
Practical Management Science
Operations Management
ISBN:
9781337406659
Author:
WINSTON, Wayne L.
Publisher:
Cengage,
Marketing
Marketing
ISBN:
9780357033791
Author:
Pride, William M
Publisher:
South Western Educational Publishing
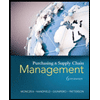
Purchasing and Supply Chain Management
Operations Management
ISBN:
9781285869681
Author:
Robert M. Monczka, Robert B. Handfield, Larry C. Giunipero, James L. Patterson
Publisher:
Cengage Learning