2. Results 2.1 Calibration Figure 2: Reacceptance magnitude for node 2 excitation and displacement response of node 2. Accelerance 2.3. Stabilisation diagram 101 Stabilization Diagram 100 102 X 596.6 Y 0.148614 15 Stable in frequency Stable in frequency and damping Not stable in frequency Averaged response function 100 200 300 400 500 600 700 800 900 1000 1100 Frequency (Hz) Figure 1: Acceleration of amplitude of mass (1.02 kg) -Calibration factor value is mostly about 0.14 je measured force is larger by ~ (1/0.1%). 2.2. Typical frequency response functions Receptance with excitation on node 2 and accelerometer on node 2 10° 2.4. 0.5 1 1.5 2.5 Frequency (kHz) Figure Natural frequencies Table shows first three natural frequencies Receptance magnitude (m/N) 10 104 106 10 10-10 Mode number 1 2 3 2.5. Mode shapes First three mode shapes plot 50 40 0 200 400 600 800 1000 1200 1400 1600 1800 2000 30 Frequency (Hz) 20 10 -10 -20 10 10 10 10 110 10 1101 3 102 3.5 Natural frequency 0.0941 0.0381 0.0885 -Mode shape 1 Mode shape 2 Mode shape 3 -30 -40 2 3 4 9 Nodes Table 3: Estimated damping ratios of the steel beam. Mode number Damping ratio (%) 1 0.0132 2 0.0077 3 0.0739 Using an instrumented impact hammer, vibrations were induced in a steel beam suspended from a frame experiment as can be seen in the next figure. The beam's response was monitored using an accelerometer. The following figure 1 shows images of the modal arrangement. Force measurement Response measurement Signal conditioner for force Signal conditioner for acceleration Data acquisition Acquisition software Force Response Figure 1: Images of the modal experiment arrangement Piezoelectric force gauge Piezoelectric accelerometer Charge amplifier Power supply and amplifier Picoscope - 4262 Picoscope version 6 Rectangular window Exponential window
2. Results 2.1 Calibration Figure 2: Reacceptance magnitude for node 2 excitation and displacement response of node 2. Accelerance 2.3. Stabilisation diagram 101 Stabilization Diagram 100 102 X 596.6 Y 0.148614 15 Stable in frequency Stable in frequency and damping Not stable in frequency Averaged response function 100 200 300 400 500 600 700 800 900 1000 1100 Frequency (Hz) Figure 1: Acceleration of amplitude of mass (1.02 kg) -Calibration factor value is mostly about 0.14 je measured force is larger by ~ (1/0.1%). 2.2. Typical frequency response functions Receptance with excitation on node 2 and accelerometer on node 2 10° 2.4. 0.5 1 1.5 2.5 Frequency (kHz) Figure Natural frequencies Table shows first three natural frequencies Receptance magnitude (m/N) 10 104 106 10 10-10 Mode number 1 2 3 2.5. Mode shapes First three mode shapes plot 50 40 0 200 400 600 800 1000 1200 1400 1600 1800 2000 30 Frequency (Hz) 20 10 -10 -20 10 10 10 10 110 10 1101 3 102 3.5 Natural frequency 0.0941 0.0381 0.0885 -Mode shape 1 Mode shape 2 Mode shape 3 -30 -40 2 3 4 9 Nodes Table 3: Estimated damping ratios of the steel beam. Mode number Damping ratio (%) 1 0.0132 2 0.0077 3 0.0739 Using an instrumented impact hammer, vibrations were induced in a steel beam suspended from a frame experiment as can be seen in the next figure. The beam's response was monitored using an accelerometer. The following figure 1 shows images of the modal arrangement. Force measurement Response measurement Signal conditioner for force Signal conditioner for acceleration Data acquisition Acquisition software Force Response Figure 1: Images of the modal experiment arrangement Piezoelectric force gauge Piezoelectric accelerometer Charge amplifier Power supply and amplifier Picoscope - 4262 Picoscope version 6 Rectangular window Exponential window
Elements Of Electromagnetics
7th Edition
ISBN:9780190698614
Author:Sadiku, Matthew N. O.
Publisher:Sadiku, Matthew N. O.
ChapterMA: Math Assessment
Section: Chapter Questions
Problem 1.1MA
Related questions
Question
write short discussion

Transcribed Image Text:2. Results
2.1 Calibration
Figure 2: Reacceptance magnitude for node 2 excitation and displacement response of node 2.
Accelerance
2.3.
Stabilisation diagram
101
Stabilization Diagram
100
102
X 596.6
Y 0.148614
15
Stable in frequency
Stable in frequency and damping
Not stable in frequency
Averaged response function
100 200 300 400 500 600 700 800 900 1000 1100
Frequency (Hz)
Figure 1: Acceleration of amplitude of mass (1.02 kg)
-Calibration factor value is mostly about 0.14 je measured force is larger by ~ (1/0.1%).
2.2. Typical frequency response functions
Receptance with excitation on node 2 and accelerometer on node 2
10°
2.4.
0.5
1
1.5
2.5
Frequency (kHz)
Figure
Natural frequencies
Table shows first three natural frequencies
Receptance magnitude (m/N)
10
104
106
10
10-10
Mode number
1
2
3
2.5.
Mode shapes
First three mode shapes plot
50
40
0
200
400 600
800
1000 1200 1400 1600 1800 2000
30
Frequency (Hz)
20
10
-10
-20
10
10
10
10
110
10
1101
3
102
3.5
Natural frequency
0.0941
0.0381
0.0885
-Mode shape 1
Mode shape 2
Mode shape 3
-30
-40
2
3
4
9
Nodes
Table 3: Estimated damping ratios of the steel beam.
Mode number
Damping ratio (%)
1
0.0132
2
0.0077
3
0.0739

Transcribed Image Text:Using an instrumented impact hammer, vibrations were induced in a steel beam suspended from a frame
experiment as can be seen in the next figure. The beam's response was monitored using an accelerometer.
The following figure 1 shows images of the modal arrangement.
Force measurement
Response measurement
Signal conditioner for force
Signal conditioner for acceleration
Data acquisition
Acquisition software
Force
Response
Figure 1: Images of the modal experiment arrangement
Piezoelectric force gauge
Piezoelectric accelerometer
Charge amplifier
Power supply and amplifier
Picoscope - 4262
Picoscope version 6
Rectangular window
Exponential window
Expert Solution

This question has been solved!
Explore an expertly crafted, step-by-step solution for a thorough understanding of key concepts.
Step by step
Solved in 2 steps

Recommended textbooks for you
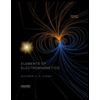
Elements Of Electromagnetics
Mechanical Engineering
ISBN:
9780190698614
Author:
Sadiku, Matthew N. O.
Publisher:
Oxford University Press
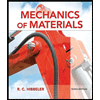
Mechanics of Materials (10th Edition)
Mechanical Engineering
ISBN:
9780134319650
Author:
Russell C. Hibbeler
Publisher:
PEARSON
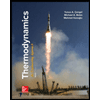
Thermodynamics: An Engineering Approach
Mechanical Engineering
ISBN:
9781259822674
Author:
Yunus A. Cengel Dr., Michael A. Boles
Publisher:
McGraw-Hill Education
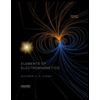
Elements Of Electromagnetics
Mechanical Engineering
ISBN:
9780190698614
Author:
Sadiku, Matthew N. O.
Publisher:
Oxford University Press
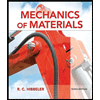
Mechanics of Materials (10th Edition)
Mechanical Engineering
ISBN:
9780134319650
Author:
Russell C. Hibbeler
Publisher:
PEARSON
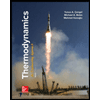
Thermodynamics: An Engineering Approach
Mechanical Engineering
ISBN:
9781259822674
Author:
Yunus A. Cengel Dr., Michael A. Boles
Publisher:
McGraw-Hill Education
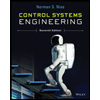
Control Systems Engineering
Mechanical Engineering
ISBN:
9781118170519
Author:
Norman S. Nise
Publisher:
WILEY
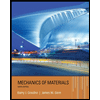
Mechanics of Materials (MindTap Course List)
Mechanical Engineering
ISBN:
9781337093347
Author:
Barry J. Goodno, James M. Gere
Publisher:
Cengage Learning
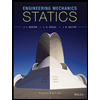
Engineering Mechanics: Statics
Mechanical Engineering
ISBN:
9781118807330
Author:
James L. Meriam, L. G. Kraige, J. N. Bolton
Publisher:
WILEY